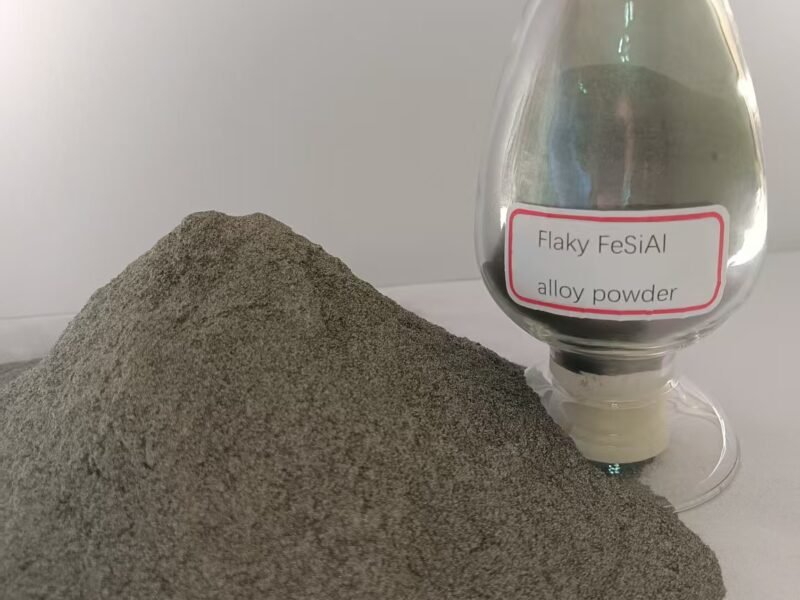
I. Product performance advantages
Flake FeSiAl (FeSiAl) absorbing powder is a soft magnetic alloy powder with iron, silicon and aluminum as the main components. Its unique microstructure and composition design give it excellent electromagnetic wave absorption performance. The main advantages are reflected in the following aspects:
1. High-frequency characteristics and low loss
FeSiAl absorbing powder has a wide bandwidth (0-20 MHz) and high magnetic permeability (μi=26-125), and still maintains low power loss (about 140 W/kg) at high frequencies, which is significantly better than traditional iron powder cores (680 W/kg). Its saturation magnetization intensity (Bs=1.05 T) far exceeds ferrite (0.5 T) and iron-nickel-molybdenum magnetic powder cores (<0.8 T), and is suitable for energy storage and high-frequency signal processing in high current scenarios.
2. Excellent temperature stability
Below 40°C, the magnetic permeability of Sendust approaches zero, and it can still maintain stable magnetic properties in high temperature environments, meeting the circuit design requirements under complex working conditions.
3. Cost-effectiveness and environmental protection
Sendust does not contain precious metals nickel (Ni) and molybdenum (Mo), and the cost of raw materials is more than 30% lower than that of iron-nickel-molybdenum magnetic powder cores, and the preparation process has an obvious trend of greening, such as enhancing the mechanical properties of flexible composite materials by regulating hydrogen bonds through water.
4. **Structural design and processability**
The flaky powder is surface treated to optimize fluidity and formability, and combined with nanotechnology, the magnetic permeability and mechanical strength can be further improved. For example, the composite film with aramid nanofiber (ANF) added has a tensile strength of 136.88 MPa at 60% ANF content, and has both high flexibility and folding tolerance.
2. Core application direction
Flake iron silicon aluminum absorbing powder has achieved large-scale application in multiple high value-added fields due to its performance advantages:
1. High-frequency electronic components
Filters and inductors: high-frequency filters used in switching power supplies and large-screen LCDs, supporting large current operation of tens to hundreds of amperes, replacing traditional ferrite materials.
Power chokes and resonant inductors: significantly reduce energy loss and improve efficiency in rectifier equipment, uninterruptible power supplies (UPS) and power factor correctors (PFC).
2. Electromagnetic compatibility (EMC) and absorbing materials
Flexible absorbing film: FeSiAl/ANF film prepared by composite nanofiber technology achieves an effective absorption bandwidth of 2.84 GHz and a reflection loss of -46.81 dB at a thickness of 3 mm, which is suitable for flexible electronic devices such as 5G communication equipment and drone radar stealth coatings.
Electromagnetic shielding materials: used in scenarios such as new energy vehicle motors and data center servers to suppress electromagnetic interference (EMI).
3. New energy and power electronics
Photovoltaic inverters and energy storage systems: improve energy conversion efficiency and reduce heat loss, support high power density design.
Electric vehicle charging piles: optimize high-frequency transformer performance, shorten charging time and reduce volume.
—
III. Market demand and development trends
1. Market driving factors
Miniaturization and high frequency of electronic products: Consumer electronics and communication equipment are evolving towards high frequency (>1 MHz), driving the demand for high magnetic permeability and low loss materials. It is estimated that the global flake iron silicon aluminum powder market will grow at an average annual rate of 8.5% from 2024 to 2030.
New energy industry expansion: The explosive growth of the global photovoltaic, wind power and electric vehicle industries has driven the demand for supporting inductor components, and China’s market share will exceed 40%.
Defense and aerospace: The demand for stealth coatings and radar absorbing materials has increased, and military applications account for about 15%.
2. Technology development trends
Nano-sizing and composite modification: Enhance the absorption performance by adding rare earth elements or carbon-based materials, and develop ultra-thin broadband absorbing coatings.
Green manufacturing process: Use water-based molding and low-temperature sintering technology to reduce energy consumption and increase material utilization to more than 90%.
3D printing and customized production: Combined with additive manufacturing technology, rapid prototyping of complex structure electromagnetic components can be achieved, shortening the R&D cycle.